April 7, 2025
Welcome to Razor Labs‘ Q1 2025 Newsletter!
We’re excited to share Razor Labs’ key achievements from Q1 2025 – a quarter defined by continued growth, innovation, and global expansion, all fueled by our commitment to operational excellence through AI.
Our momentum continues to build across the mining sector and beyond, spanning continents and milestones – from industry awards and events to new partnerships and on-site success stories.
Global Growth
Razor Labs Enters Subscription Agreement with SIMEC Mining Following Initial Pilot Phase
John Stewart, Chief Engineering & Reliability at SIMEC Mining, commented:
“The initial stages of implementing DataMind AI™ have shown potential in enhancing our site’s operations. By providing early warnings and actionable insights, we aim to prevent equipment failures before they occur, significantly reducing unplanned downtime and maintenance costs. DataMind AI™ also helps us maintain a safer working environment by minimizing the need for manual inspections in hazardous areas. We are optimistic about the continued benefits that this technology will deliver.” Read more>>
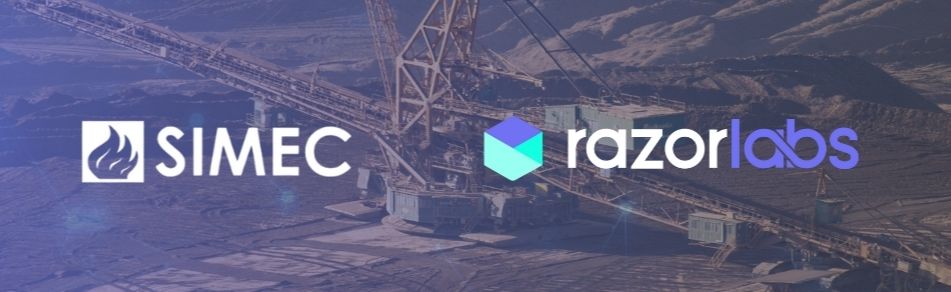
Industry Recognition 🏆
Unleashing the Next Generation of Predictive Maintenance
We’re honored to be recognized for the second year in a row, taking home the Mining Technology Award in Innovation Award for Equipment Diagnostics.
“This recognition is a strong validation of DataMind AI™’s impact on the mining industry. Our team continues to push boundaries, helping clients increase efficiency and reliability while reducing operational risk.” – Tomer Srulevich, CBO at Razor Labs. Read more >>
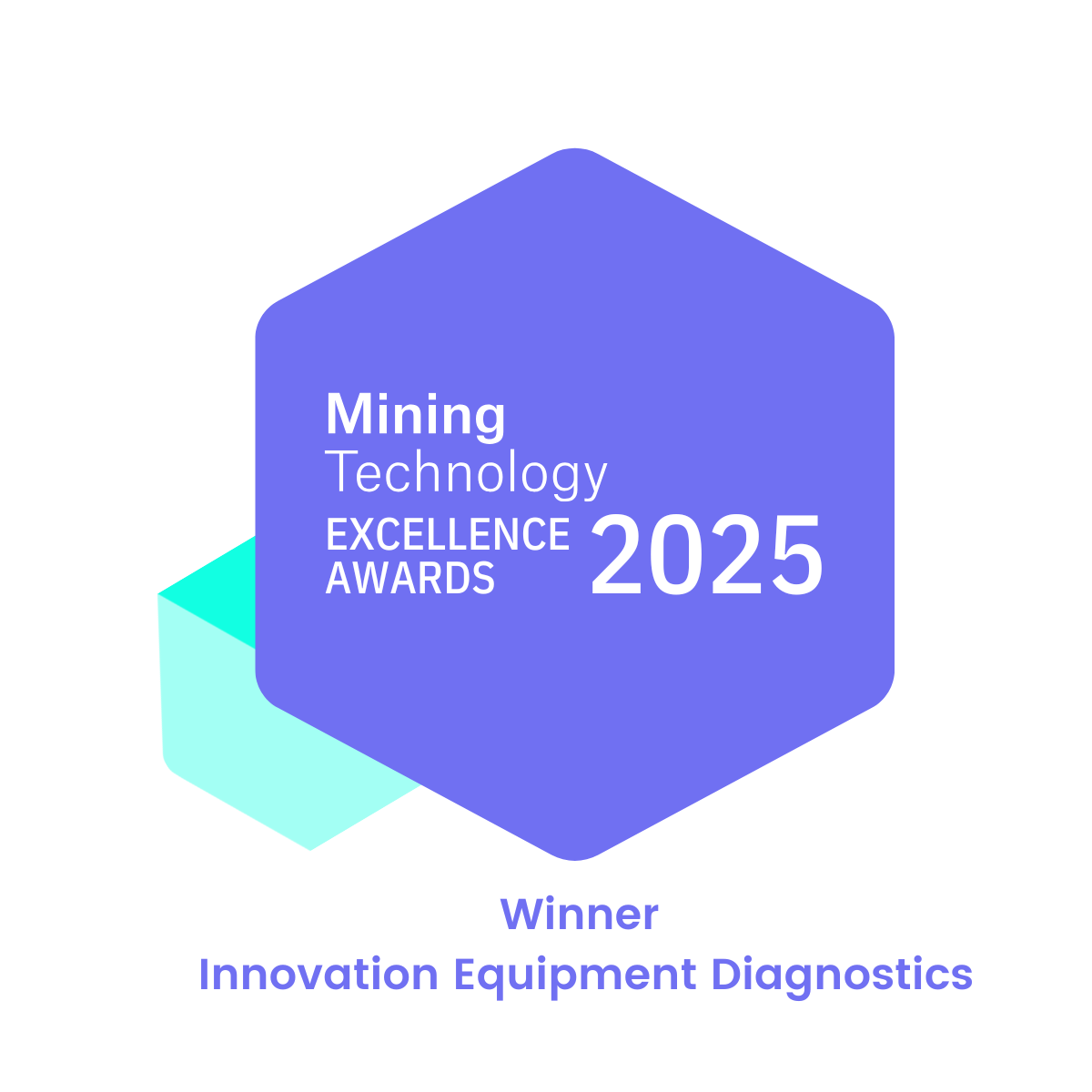
Impact from the Field
This quarter, our AI-powered predictive maintenance platform – DataMind AI™ helped clients around the world prevent failures, reduce downtime, and improve operational performance. Here are a few of the selected real-world examples from Q1 2025 that show how data-driven maintenance delivers results:
DataMind AI™ Detects a Critical Centrifuge Drum Imbalance
Unplanned downtime prevented: 6 hours
Estimated loss savings: $271,560
Download the full case study here>>
DataMind AI™ Prevents Sinter Fan Failure by Detecting Lubrication Issues & Mechanical Looseness
Unplanned downtime prevented: 7 hours
Estimated loss savings: $455,000
Download the full case study here>>
DataMind AI™ Detects Hidden Pump Issues and Prevents Costly Shutdowns
Unplanned downtime prevented: 6 hours
Estimated savings: $195,000
Download the full case study here >>
DataMind AI™ Identifies Gearbox Tooth Damage in Ball Mill, Ensuring Operational Continuity
Unplanned downtime prevented: 9 hours
Estimated savings: $432,000
Download the full case study here >>
Webinar on Demand
Razor Labs hosted a live session with Austmine, titled “Real-Life Examples of AI Sensor Fusion Predictive Maintenance”. The webinar showcased real-world applications of DataMind AI™ across global mining operations. Watch the full webinar >>
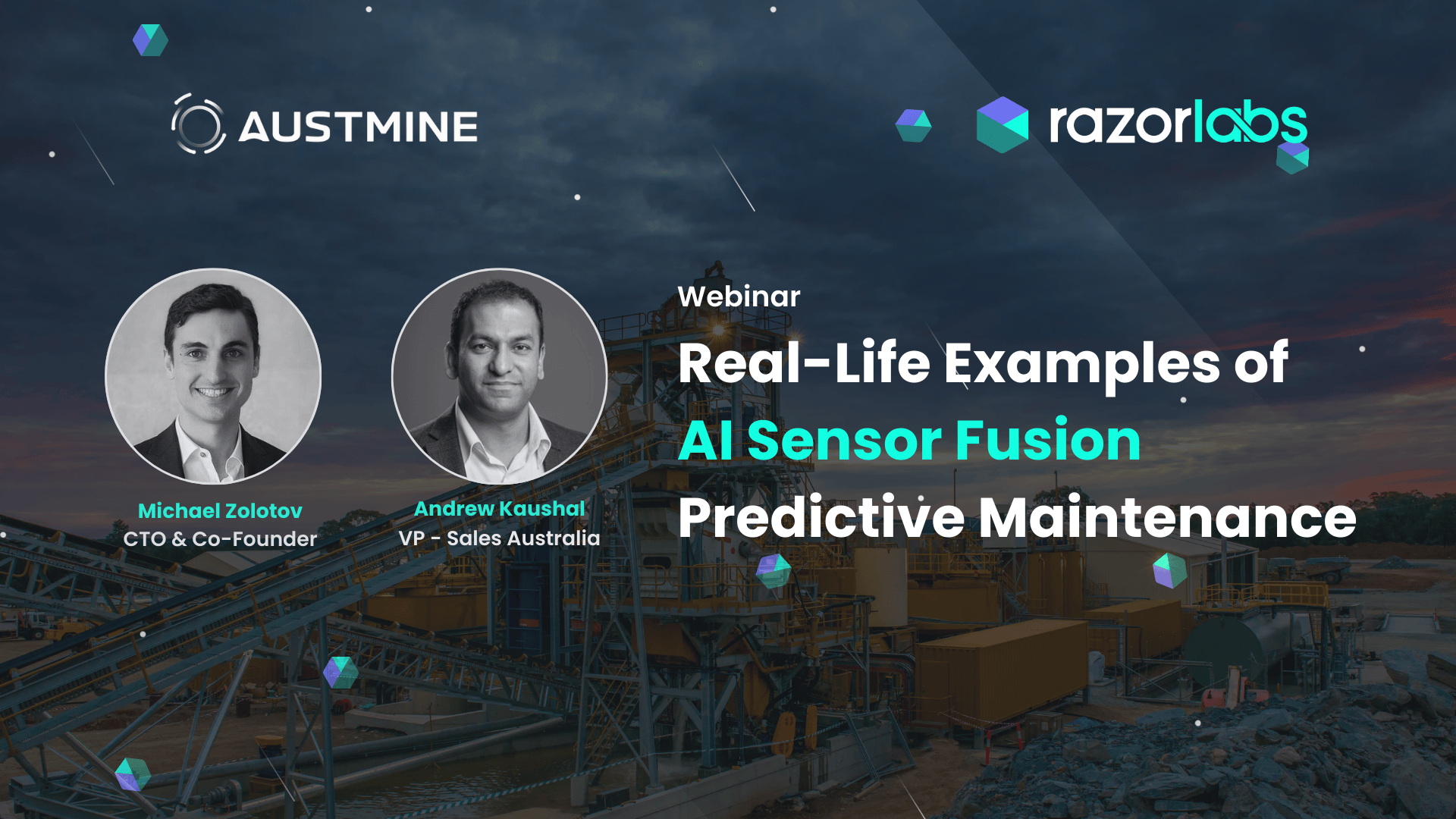
Industry Events
🇿🇦 Mining Indaba 2025
Razor Labs attended the Investing in African Mining Indaba 2025 in Cape Town from February 3 – 6. The event provided opportunities to connect with industry leaders and discuss advancements in mining technology. Read more >>
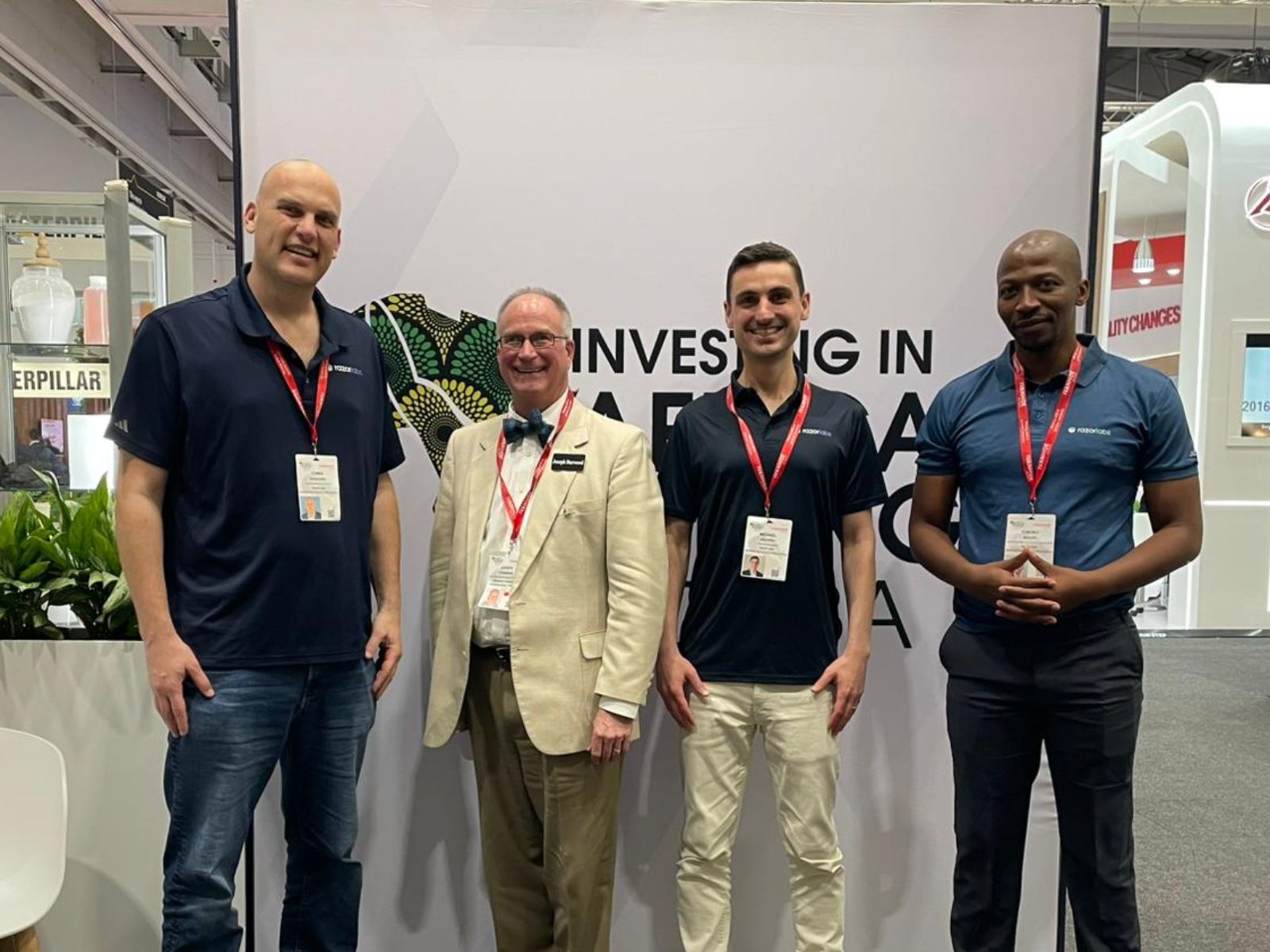
🇦🇺 Austmine Innovation Roadshow
Razor Labs participated in the Austmine Mining Innovation Roadshow, where industry leaders gathered to explore the latest innovations shaping the future of mining. Read more >>
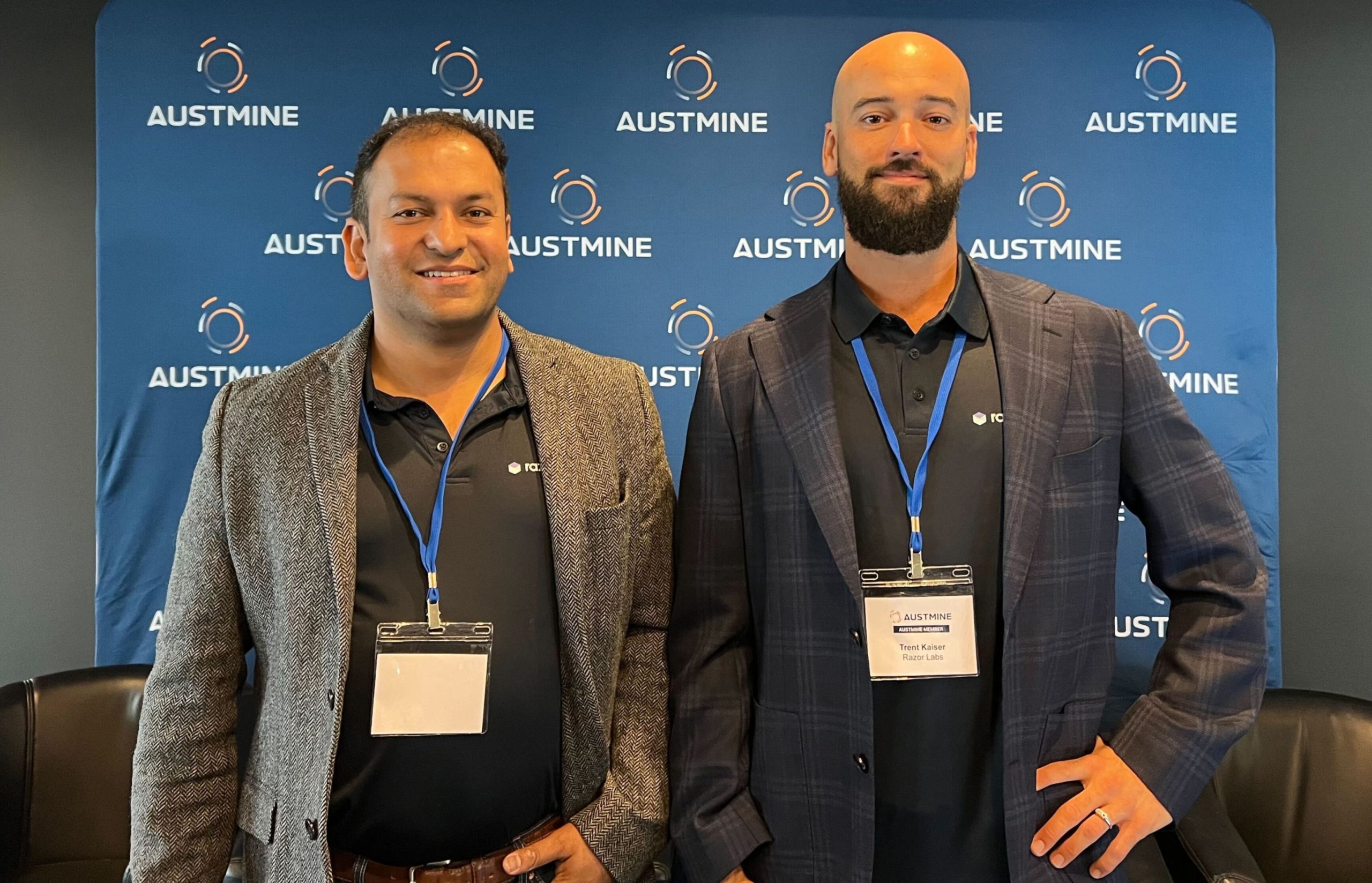
🇿🇲 Zambia Innovation Mission
Razor Labs participated in Austmine’s mining mission to Zambia, The delegation engaged with mining and energy stakeholders across the Copperbelt Province and visited key operations sites. Read more >>
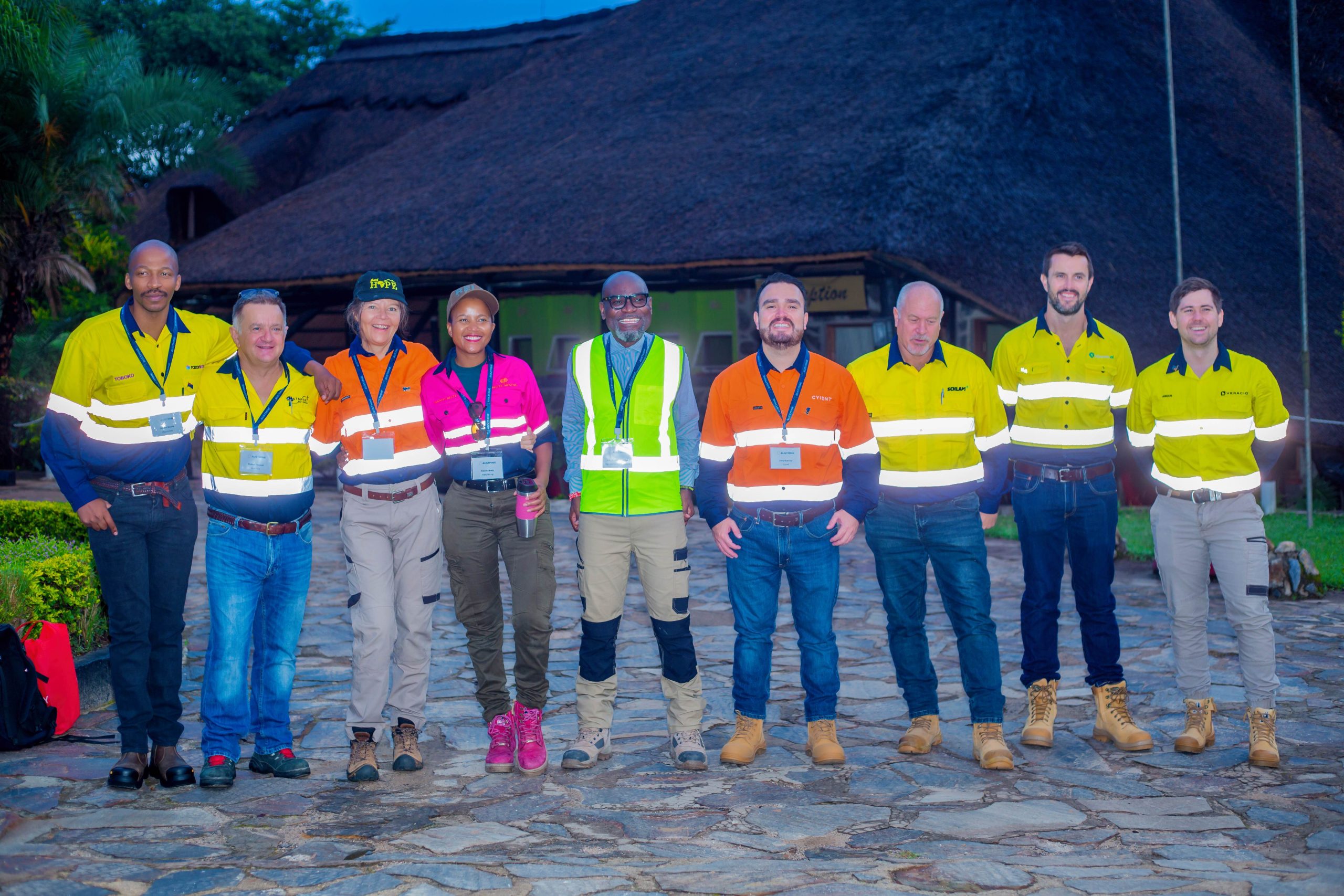
Razor Labs Expert Series
In this episode, we dive into the fascinating world of AI-driven innovation in mining with David Refael, Head of R&D at Razor Labs. From his unique leadership approach to building and scaling the company’s largest department, to real-world applications of AI and vibration analysis in predictive maintenance, the conversation covers both the technical and human sides of innovation. You’ll hear how Razor Labs collaborates with sensor manufacturers, fosters a culture of creativity, and pushes the boundaries of what’s possible in industrial AI.
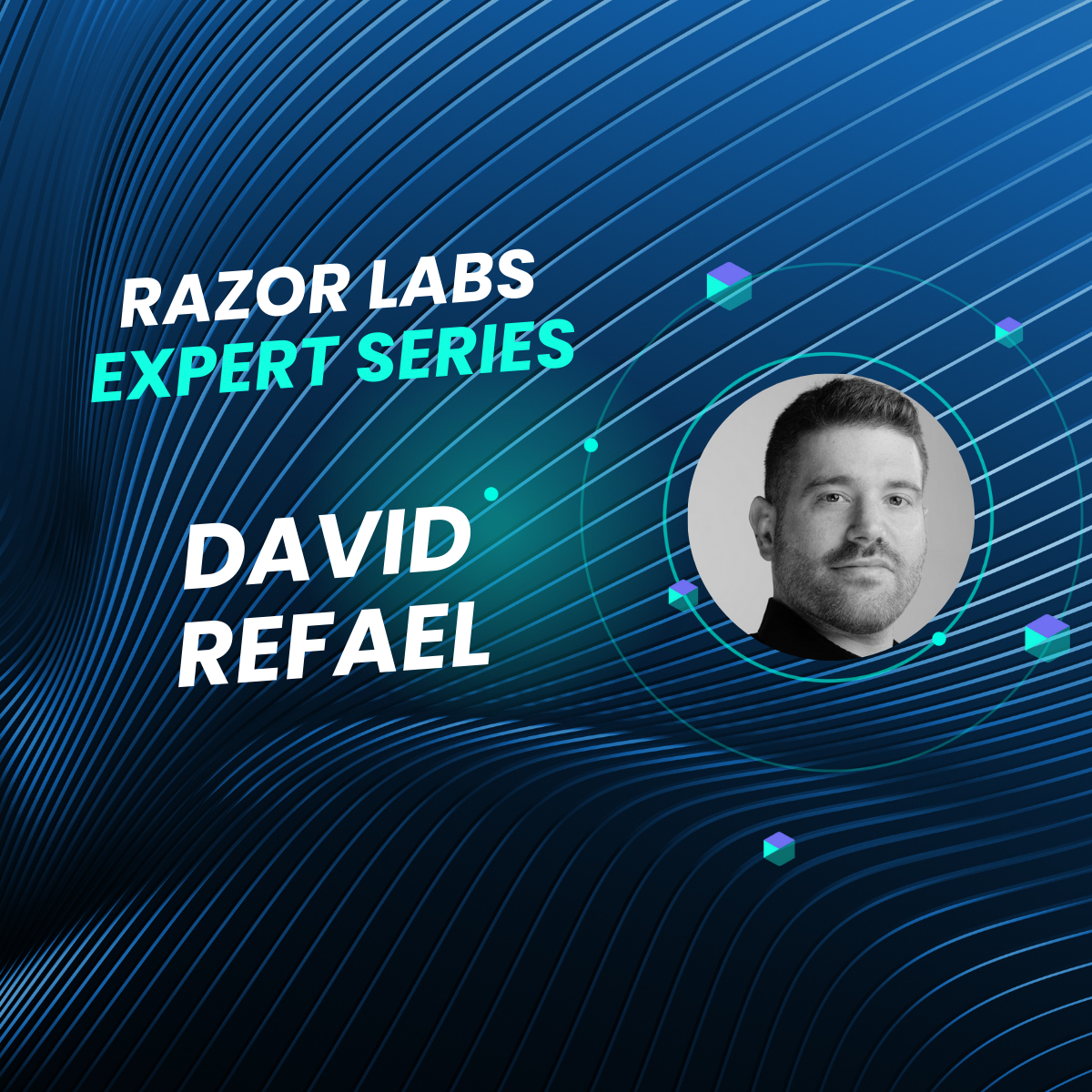