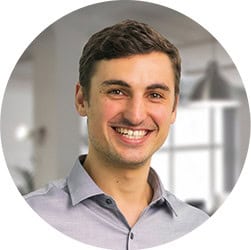
January 5, 2023
Although the potential is immense, studies show that most Predictive Maintenance programs fail to drive real value for mining companies.
In this blog, I will discuss three common myths about predictive maintenance and how mining companies can leverage AI sensor fusion to transform their predictive maintenance programs into value drivers.
Myth 1. The data collected by the mining companies can be easily used for Predictive Maintenance
Myth 2. Models that predict failures give (enough) value.
Myth 3. Deploying sensors is enough for Predictive Maintenance.
In Part 1 of this blog series, I discussed the first and most common misconception that prevents the majority of Predictive Maintenance programs from delivering real value to mining companies – “The Big Data that mining companies collect can be easily leveraged for Predictive Maintenance.”
We have seen that the collected data doesn’t come from the right sources and is inefficient in running proper root cause analysis that can prevent unplanned shutdowns or recurring failures. This post will discuss the second prevailing belief.
Myth 2. Models that predict failures provide (enough) value
Most failures require different maintenance actions to prevent downtime. Prescribing a specific maintenance action is critical for value realization.
The mining companies’ data science teams are tasked with building models that predict machine failures. Even when designed successfully, they can’t provide the necessary value. Mining machinery is highly complex, and even when the models successfully predict malfunctions, more insights are required to manage them. After all, our goal is not only to predict a malfunction but to prevent the shutdown from happening and the subsequent shutdowns later on.
Additionally, we are looking to prescribe a specific maintenance action to avoid this shutdown, deriving value from the Predictive Maintenance model that translates into fewer failures, fewer unexpected shutdowns, fewer work orders, and increased throughput and safety.
The multitude of potential failure causes
Let’s take a look at the possible failure causes. As discussed in Part 1, the existing Predictive Maintenance solutions are based on machine reports. It can be a vibration-based report, oil-based report, thermography, or a model developed by the data science teams. A report will identify a fault in a machine, for example, bearing wear. The complexity of the problem is that many maintenance actions can be performed depending on the root cause.
Illustration 1 displays possible reasons for the wearing bear failure:
- Overload
- Oil contamination
- Imbalance in the conveyor belt strap
- Lubrication failure.
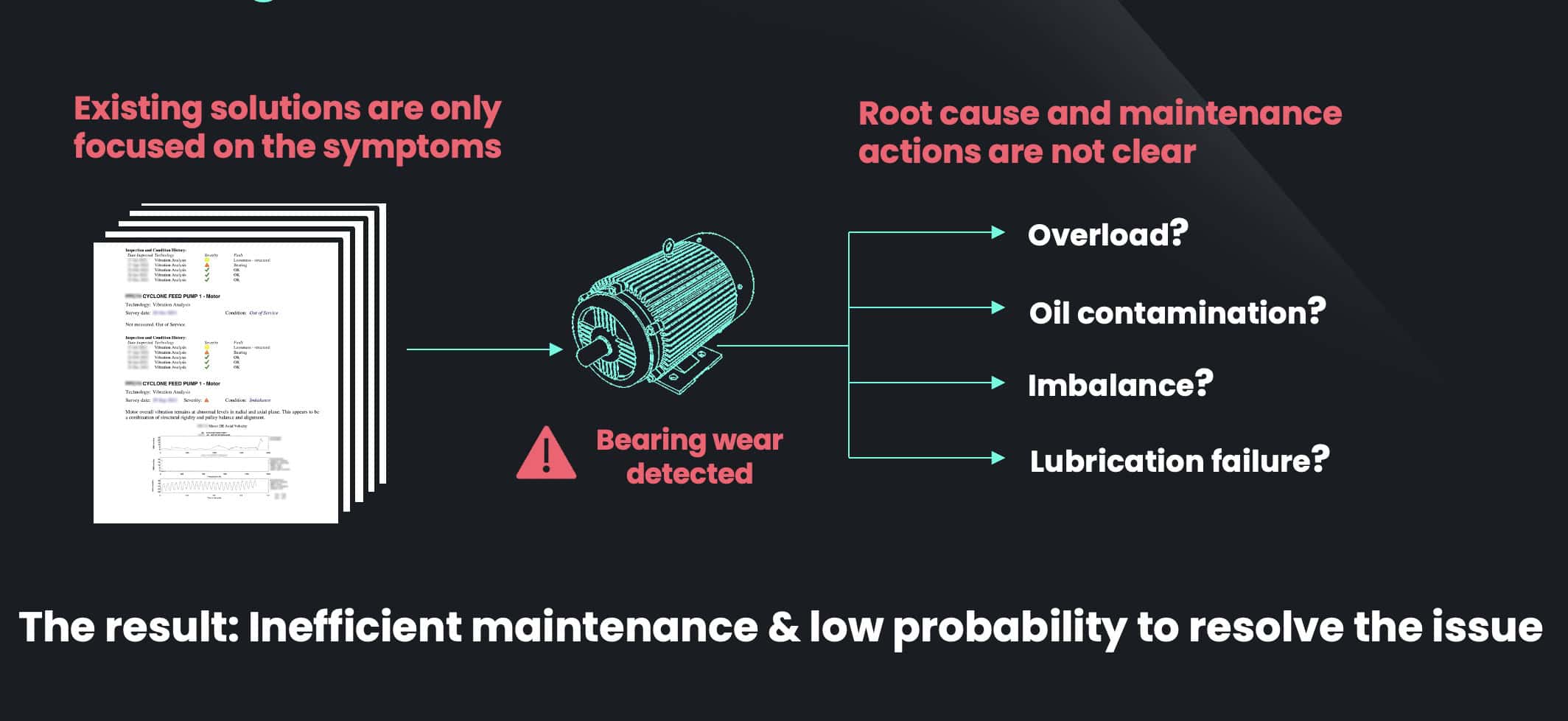
Illustration 1. Current Predictive Maintenance Solutions
Each of these root causes will trigger a different maintenance action to treat the failure properly. As long as we do not have a reference to the specific maintenance action required, the likelihood of treating the cause of the problem itself is very low.
When a machine malfunctions, the existing solutions don’t uncover the actual root cause of the failure, and the only thing that is treated is the symptom of the problem, perpetuating the ongoing loop of recurring machine failures.
In the illustrated example, if we address the symptom – replacing the bearing, the failure will happen again, and the cycle will continue, imposing two significant threats:
- Inefficient maintenance – flooding the maintenance teams with work orders and causing them to chase their tails
- Potential safety hazard – placing the maintenance team in the proximity of faulty machines in a critical health state.
Treating the underlying failure cause, not the symptom
Treating the underlying failure cause can prevent the malfunction from recurring, lowering the total number of malfunctions and thus increasing equipment reliability, the MTBF, and the safety of the staff.
This can be achieved by a solution that fuses all the data sources and uncovers the root cause of the failure – in this case – lubrication failure and prescribes a specific maintenance action, e.g., “Check the ALS system and relubricate bearing.” (Illustration 2)
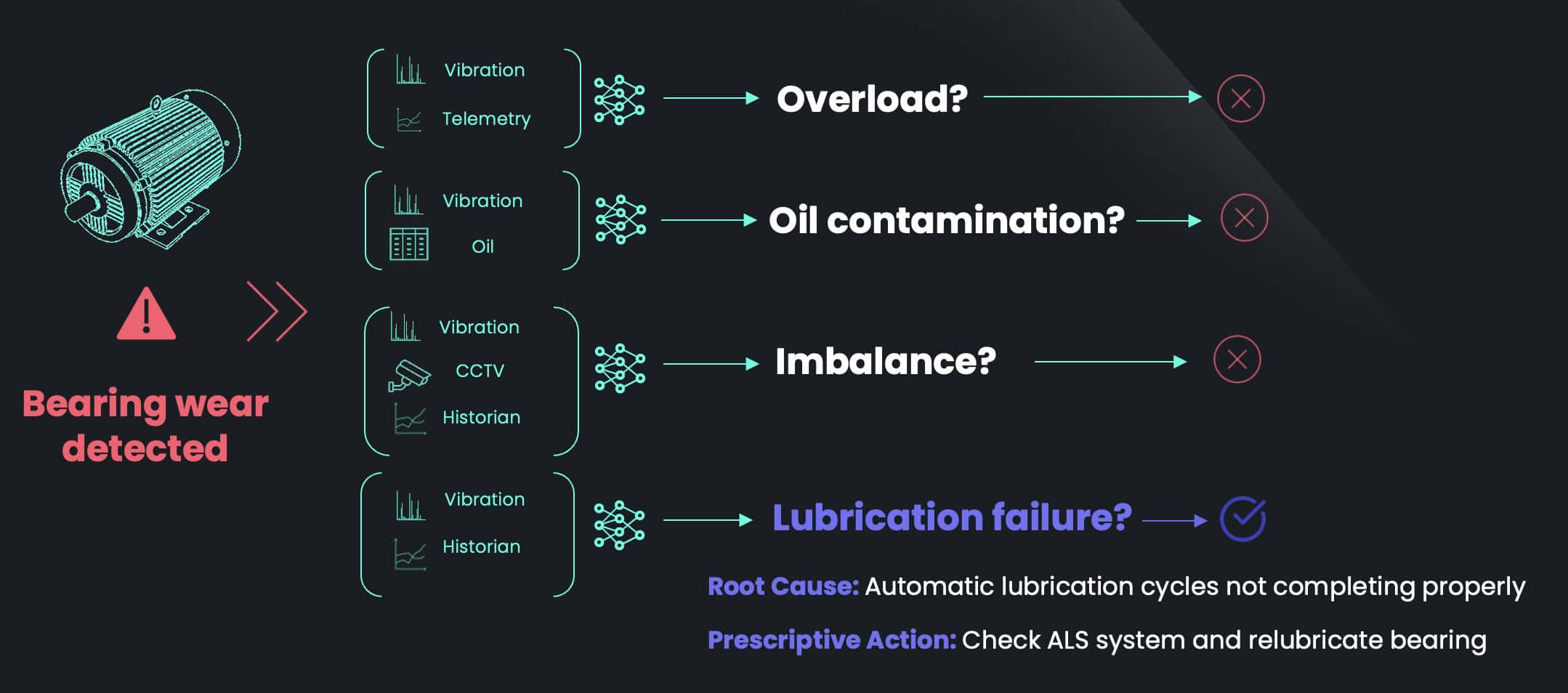
Illustration 2. Identifying the root cause of failures and prescriptive actions
In conclusion, it is important for mining companies to go beyond just predicting failures and instead prescribe specific maintenance actions in order to increase reliability and safety, prevent downtime, and break the cycle of recurring failures. This requires a solution that fuses all data sources and is able to properly identify the root cause of failures. By addressing the root cause and prescribing the appropriate maintenance action, mining companies can improve the value of their predictive maintenance programs and drive better outcomes.
In Part 3 of this blog series, I will discuss Myth #3 – the assumption that Deploying sensors is enough for Predictive Maintenance. Stay tuned.