Vibration Analysis in Mining: Why Going Beyond Traditional Methods Matters
July 14, 2025
DataMind AI – Vibration Analysis System That Unlocks Hidden Faults in Mining Equipment
Vibration analysis is one of the most powerful tools in mining predictive maintenance – not just for detecting symptoms, but for delivering accurate diagnostics that point directly to failure modes.
In mining environments, machines operate under variable operational conditions – including changing loads, fluctuating duty cycles, and substantial ambient noise. These challenges introduce significant interference into vibration signals, making it harder to detect faults or causing unnecessary false alarms.
That’s why DataMind AI™ was purpose-built for mining, with three critical vibration analysis differentiators:
- Operational Mode Isolation – monitoring the machine in real time and continuously compares vibration signals under stable load (motor current) and speed conditions – something that’s impractical with manual recordings. By combining vibration data with motor current and tachometer input, the system filters out the influence of changing operational conditions and reveals the true mechanical fault signals.
- Envelope Demodulation – performing intelligent filtering in the spectral domain, removing frequency components that are not related to machine degradation. This eliminates much of the operational noise and makes emerging fault patterns clearer and easier to detect – often earlier than traditional methods, and sometimes uncovering issues that would otherwise go unnoticed.
- Root Cause Diagnostics through Vibration, Oil, and Operational Sensors Correlation – cross-referencing vibration data with oil condition and operational mode to isolate the true root cause of faults.
These capabilities allow DataMind AI™ to detect faults earlier and more reliably, reducing risk and extending equipment life across mills, crushers, pumps, compressors, fans, and other critical equipment.
Why Vibration Analysis Matters in Mining
Why Vibration Analysis Matters in Mining
Vibration analysis is the most sensitive method for detecting mechanical issues in rotating machinery. Even small deviations in vibration patterns can signal early signs of misalignment, imbalance, or bearing wear.
For critical mining equipment, it enables earlier and more precise detection compared to traditional methods – reducing unplanned shutdowns, avoiding catastrophic failures, and extending asset life.
Time-based monitoring methods like temperature or pressure only reveal symptoms – not root causes – and often miss early-stage faults entirely. Many bearing failures, for example, occur without any temperature rise, or show changes only hours before breakdown.
Vibration analysis, on the other hand, provides direct insight into the exact failure mode and location months before failure, offering the lead time needed to prevent downtime.
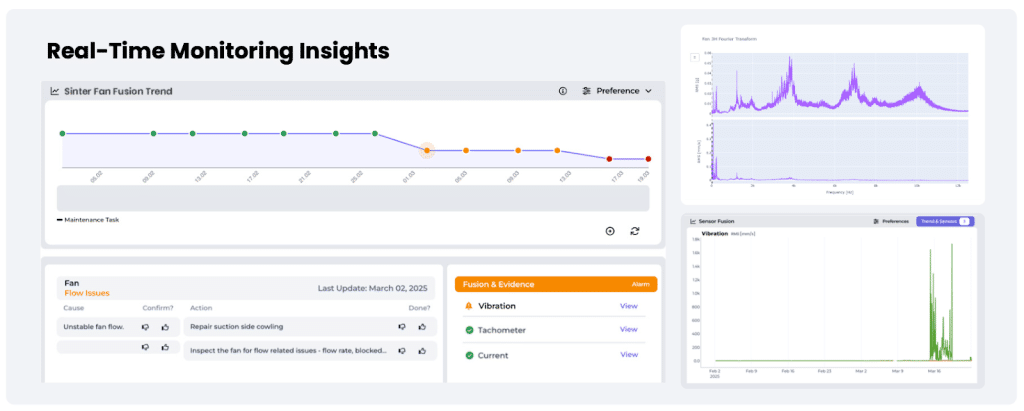
Live fault detection and diagnostics powered by DataMind AI™ vibration analysis
Advanced Vibration Analysis and Remote Sensor Coverage
Using rugged, high-bandwidth remote vibration sensors, DataMind AI™ captures complete vibration spectra across a wide frequency range – including low-speed assets under 60 RPM. This enables comprehensive vibration condition monitoring of:
- Mills (Ball, SAG, AG)
- Crushers (Jaw, Cone, HPGR)
- Conveyors
- Pumping Systems (Centrifugal, Rotary, Reciprocating)
- Compressors
- Fans & Blowers (ID, FD, Sinter, Cooling Towers)
- Rotating Machinery (Screens, Kilns, Rolling Mills)
- Other Critical Plant Equipment
With always-on connectivity, sensor data is streamed in real time to the cloud for fusion and analysis – eliminating the need for manual readings or spot checks.
Each sensor is engineered for harsh environments and performs reliably in areas with dust, moisture, vibration, and electromagnetic interference. This robustness ensures uninterrupted data flow and actionable alerts.
To enable precise diagnostics, systems must capture the full vibration spectrum, not just RMS values. That’s why DataMind AI™ uses gateways with sampling frequencies optimized for mining – including for slow, noisy, and variable-load machines.
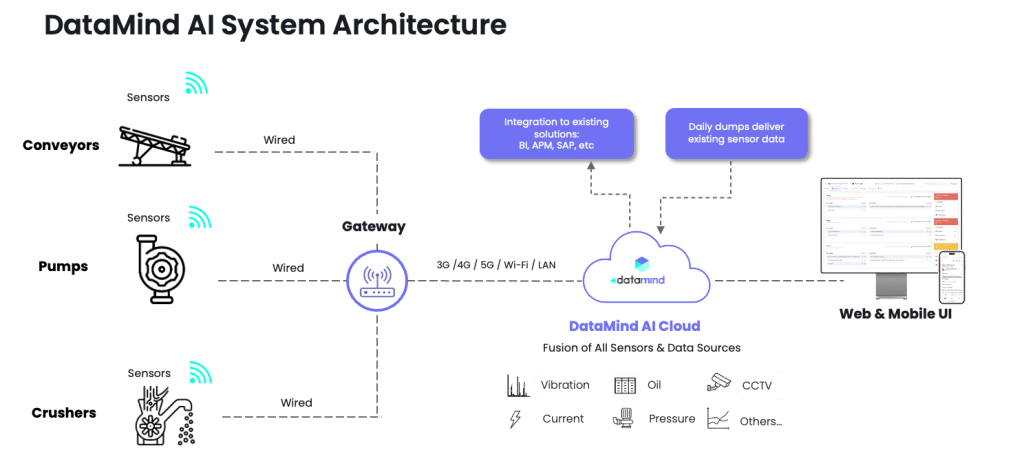
DataMind AI™ System Architecture: Sensors → Gateway → Cloud → Insights.
Differentiator 1: Operation MODE Mode Isolation for Mining Conditions
Mining equipment operates under highly variable conditions ‐ with frequent fluctuations in load and speed. These changes can distort vibration signals, either masking real faults or generating false alarms.
DataMind AI™ overcomes this by isolating the asset’s Operational Mode, using additional sensor data like motor current and speed (tachometer). By correlating vibration readings to the actual working state of the machine, the system can tell the difference between a legitimate increase in workload and a sign of mechanical deterioration.
This enables early and accurate fault detection ‐ even in environments where vibration alone would be unreliable.
Differentiator 2: Envelope Demodulation for Noisy Mining Environments
Mining machines are inherently noisy – they grind, crush, and process heavy material under harsh, variable conditions. In such environments, weak failure signals often get buried under operational noise, making early detection nearly impossible using traditional vibration methods.
DataMind AI™ applies Envelope Demodulation – an advanced signal processing technique that filters out irrelevant frequencies and amplifies the faint signals that truly matter. This allows the system to identify faults that other methods miss, and to do so significantly earlier.
With Envelope Demodulation, DataMind AI™ delivers:
- Detection of deteriorations not picked up by traditional testing
- Earlier identification of bearing faults and gearmesh anomalies
- Clear signal patterns even in high-noise, low-SNR environments like crushers and mills
- Prevention of false alarms by ignoring vibration caused by normal process variation
This capability is especially valuable in mining, where standard RMS-based analysis often fails. By removing the masking effects of fluctuating load and speed, DataMind AI™ uncovers the real fault signatures hiding in the noise.
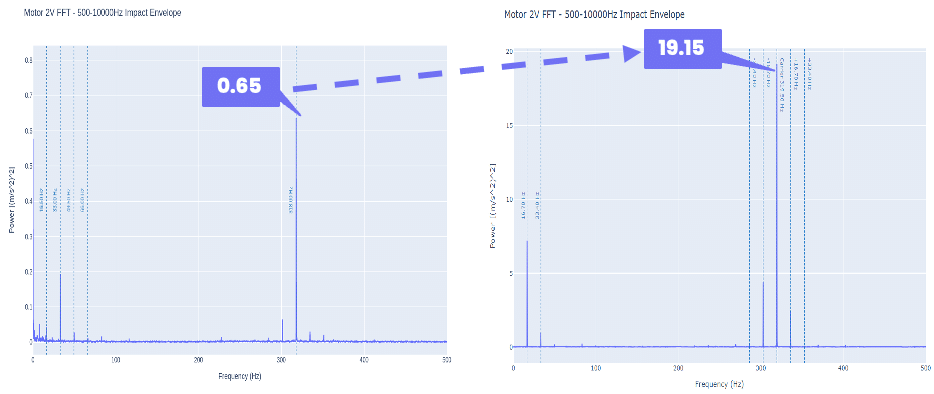
Envelope Demodulation reveals early-stage fault signal
Differentiator 3: Root Cause Diagnostics via Vibration, Oil, and Operational Mode Correlation
DataMind AI™ uses cross-domain diagnostics – combining vibration signals, oil condition data, and operational mode parameters (e.g. temperature, pressure, flow) — to pinpoint the true root cause of equipment failures.
For example, when abnormal friction is detected, oil sensors can reveal if the lubricant is contaminated, pointing to internal wear. But if oil quality is normal and motor current or camera input shows increased load, the issue may stem from operational overload – such as excessive ore feed.
This integrated view ensures that maintenance teams respond to the actual problem, not just the symptom – helping avoid unnecessary part replacements, reduce downtime, and focus intervention where it matters.
What Types of Mechanical Faults Can Be Detected with Vibration Analysis?
DataMind AI™ identifies a wide range of mechanical issues – even under complex, fluctuating conditions, such as:
- Imbalance
- Structural looseness
- Misalignment
- Bearing deterioration
- Fluting
- False brinelling
- Resonance
- Pump cavitation
- Flow issues of pumps and fans
- Gearmesh
This level of insight helps teams focus on the real underlying issue – not just symptoms – and take action early, before failures escalate.
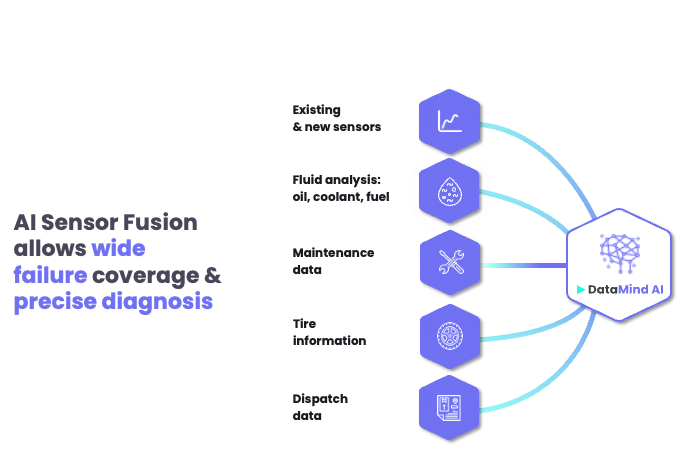
Sensor fusion for precise diagnostics
Not Just Raw Data – Automated, Actionable Diagnostics
A major challenge in vibration analysis is that it typically requires deep expertise to interpret raw signals and translate them into real mechanical insight.
DataMind AI™ eliminates that barrier. The platform delivers automated, AI-driven diagnostics that go far beyond waveform charts or RMS alerts – pinpointing:
- Specific failure modes (e.g. bearing outer race damage)
- The root cause of the problem (e.g. false brinelling)
- The severity and urgency of intervention
Each alert is based on a full-spectrum analysis and contextualized with operational mode, so maintenance teams receive not just raw data – but clear, trusted guidance on what’s happening, where, and what to do next.
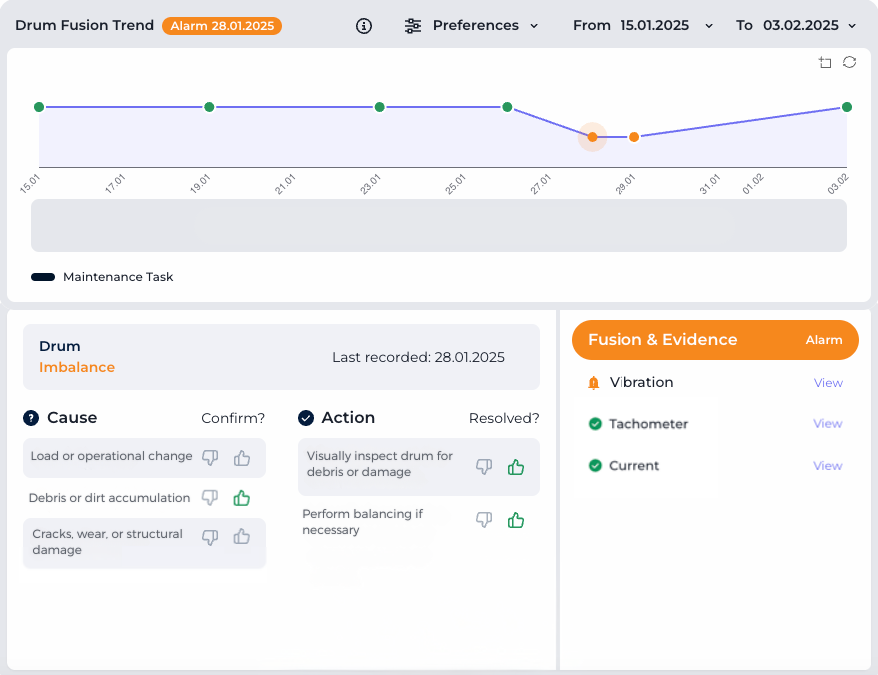
DataMind AI™ displays AI-driven fault cause, action, and sensor evidence
Real Results: Vibration Analysis Case Studies in Mining
Ball Mill Motor Bearings
DataMind AI™ identified rapid outer race deterioration in the motor bearing, missed by traditional monitoring. Advanced vibration analysis enabled early intervention – preventing 36 hours of downtime and saving $648K.
Stacker Conveyor Pulley
Vibration signals revealed early-stage bearing failure, confirmed and resolved during planned maintenance. Avoided 14 hours of unplanned stoppage and prevented a $1.12M loss.
Compressor Gearbox
Sensor fusion detected abnormal gear friction due to faulty lubrication. The issue was addressed before failure — saving 30 hours of downtime and $540K in potential losses.
In each case, DataMind AI™ provided early, accurate insights that eliminated guesswork – allowing teams to schedule the right intervention at the right time. This has prevented catastrophic failures, optimized resource allocation, and delivered full ROI within months.
Explore DataMind AI™: The Future of Vibration Analysis for Mining Equipment
Experience the benefits of next-generation vibration analysis software ‐ combining AI-powered diagnostics, full-spectrum sensors, and real-time insights tailored for mining environments.